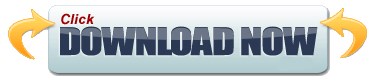
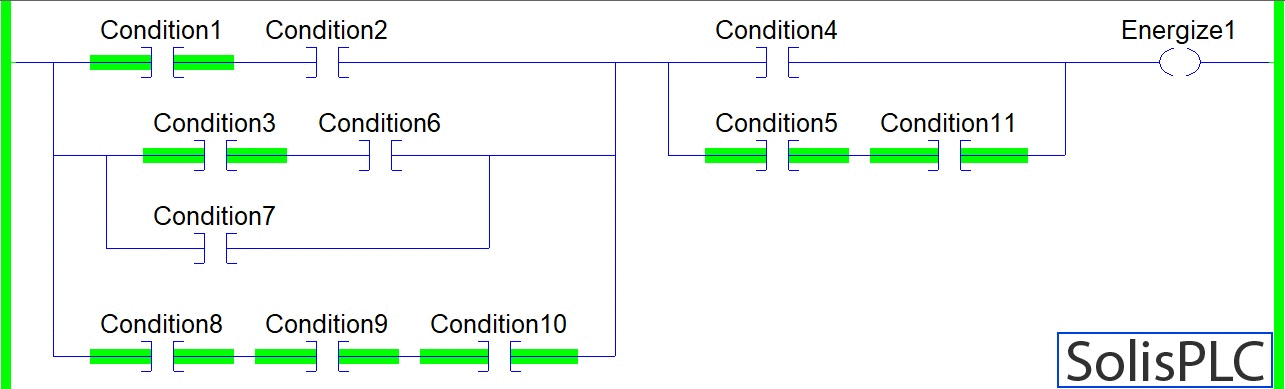
In order to show the applicability of proposed method, an UML-based tool for the design and generation of ladder code is also developed. Last part deals with automatic generation of ladder code from the validated design result.

During the execution of simulation model, factory automation (FA) engineers can evaluate the system performance and validate the PLC control logic simultaneously. By using the results of O-O design model, an O-O simulation model is constructed and is executed. Second part is concerned with O-O simulation method for validating designed ladder control logic.
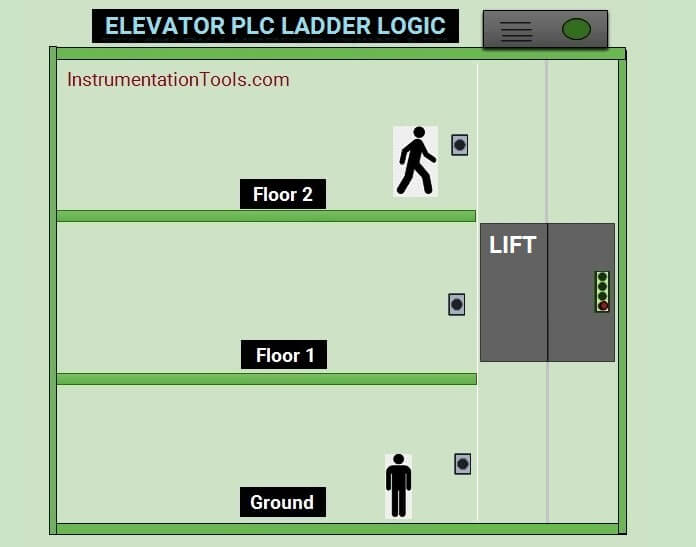
O-O design model consists of three models: functional model, structure model and interaction model. Proposed framework, as depicted in Figure 1, consists of three parts: first part deals with UML design of PLC-based control system. The main objective of this chapter is to propose an object-oriented (O-O) ladder logic development framework integrating design, validation and automatic generation of ladder logic using extended UML (Unified Modeling Language). Therefore, current PLC ladder programming practices require a more integrated way to design, simulate, and generate the ladder control logic. However, since current simulation methods have mainly focused on the overall performance evaluation of manufacturing systems such as factory layouts, resource utilization, and throughput time, they have limitations with regard to the modeling capabilities of detail logic for the input/output signal-level control of AMS. Among many validation methods, computer simulation methods are widely used because mathematical formalisms have a problem of solution space explosion as the size of system increases. To generate error-free ladder code, it is also essential to validate the designed control logic of an AMS in an effective way. To deal with these frequent configuration changes of modern manufacturing systems, it is required that logic code can be generated automatically from the design results without considering complicated control behavior. Moreover, fast customer requirement changes requires flexibility of manufacturing system. So, the control logic design phase is usually omitted in current PLC programming development life cycle though it is essential to reduce logic errors in an earlier stage of automation projects before the implementation of control logic. However, currently there are no widely adopted systematic logic code development methodologies to deal with PLC based control systems in the shop floor. To cope with these challenges, a new effective and intuitive method for logic code design and generation is needed. More recently, manufacturing trends such as flexible manufacturing facilities and shorter product life cycles have led to a heightened demand for reconfigurable control systems. Currently, programmable logic controllers (PLC) are mostly adopted as controllers of automated manufacturing systems (AMSs), and the control logic of PLC is usually programmed using a ladder diagram. Among their endeavor to overcome the obstacles, one of the frequently prescribed remedies for the problem of decreased productivity and declining quality is the automation of factories ( Zhou & Venkatesh, 1999).Īs the level of automation increases, material flows and process control methods of the shop floor become more complicated.

Most enterprises are struggling to change their existing business processes into agile, product- and customer-oriented structures to survive in the competitive and global business environment.
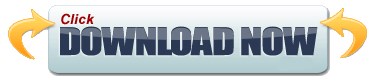